
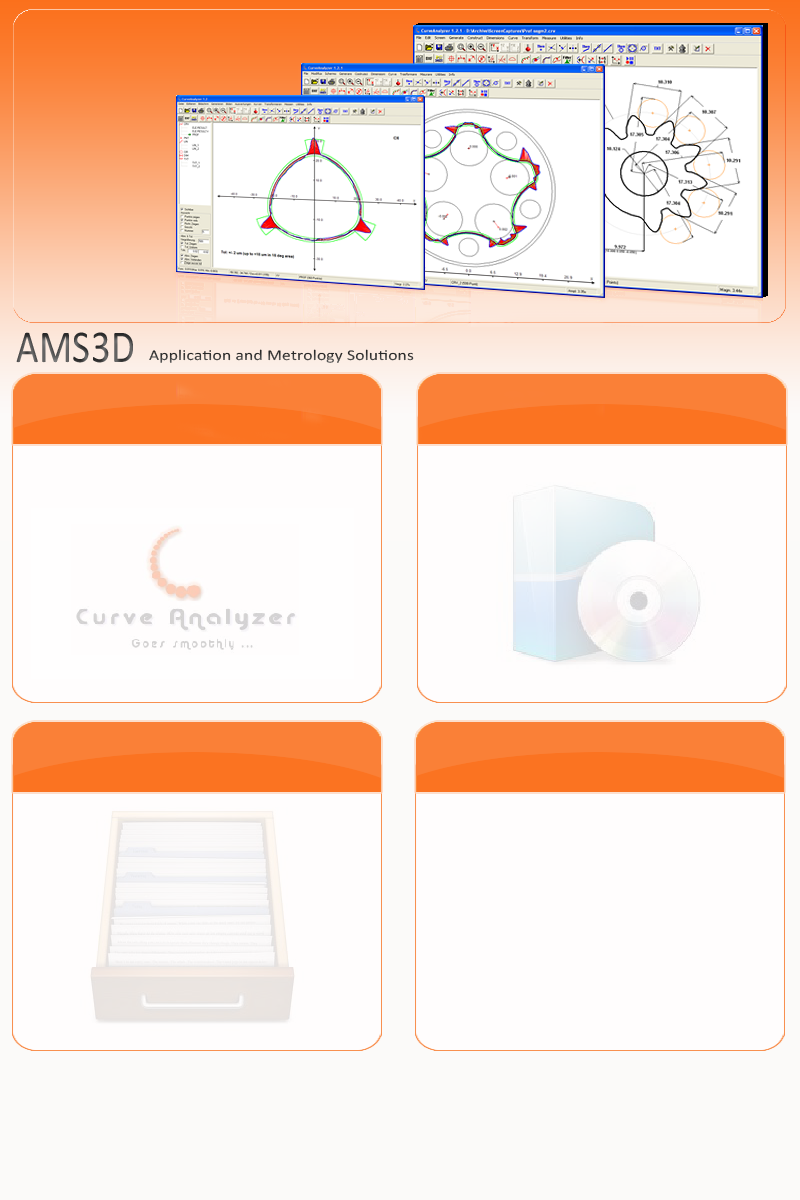
The outer fiber is subjected to tensile stress, while the inner fiber is subjected to compressive stress during bending. Metal parts must rebound during elastoplastic forming. The bending forming process of sheet metal refers to the method of forming the sheet metal under the action of applying external force by using the elastic-plastic characteristics of the material. Finally, through the bending experiments of four models, the feasibility of the iterative compensation mechanism of curvature in the continuous curvature plane bending process is verified, and different models are selected to clarify that the method has the characteristics of generality, that is, it will greatly improve the flexibility of the bending process in industrial applications without the limitation of material types and mechanical models. The bending forming simulation was carried out based on the above iterative compensation mechanism. The two materials of 304 stainless steel and ST12 cold rolled steel were studied, and the two-dimensional plane stress-strain model Abaqus cantilever beam was established by using finite element software.
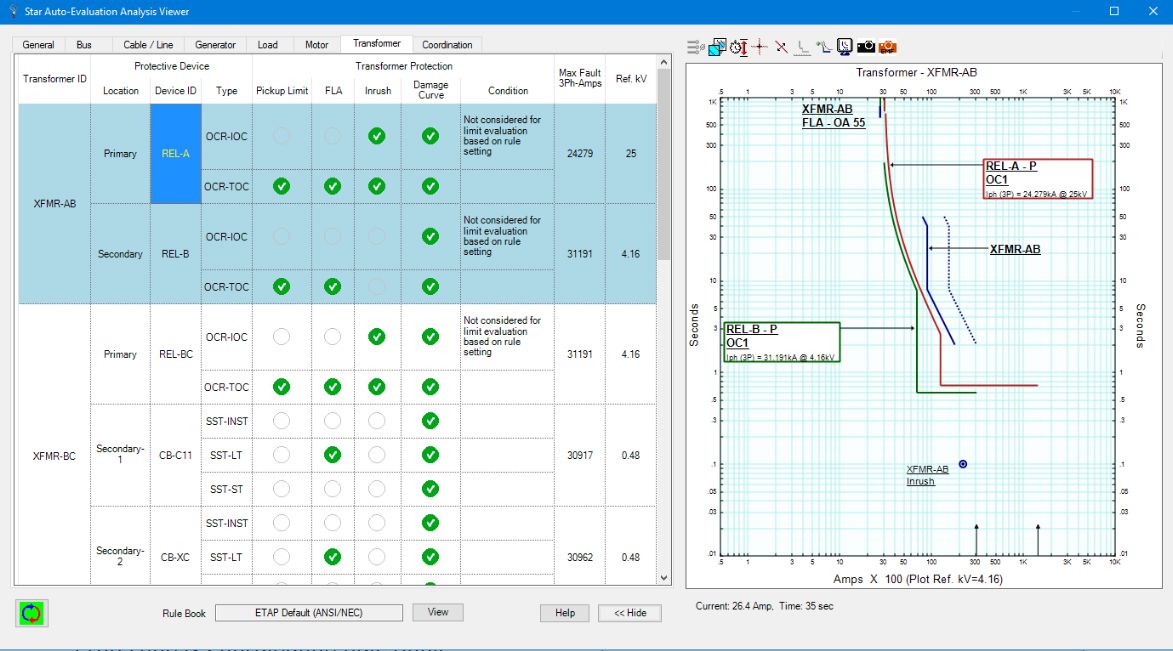
The reliability of the proposed iterative compensation method in the bending process engineering application is verified by combining simulation with experiment.
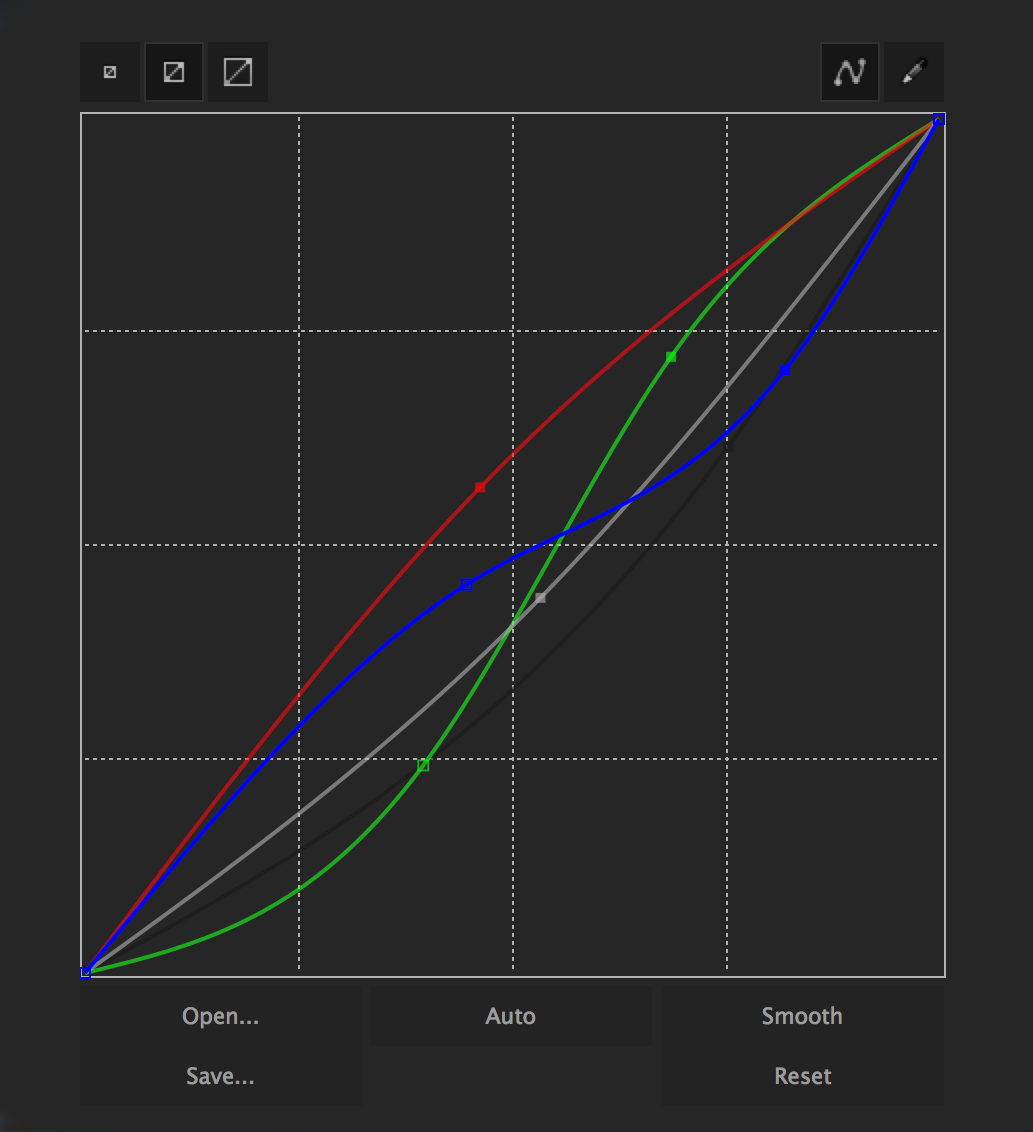
On the basis of establishing this iterative compensation mechanism, the convergence of curvature iteration in the general free bending process is proved. The purpose of this study is to take curvature as an iterative parameter and make the shape size reach the expected value through the finite compensation. Therefore, a new method for iterative compensation of bending springback with certain generality is proposed for continuous curvature bending. In recent years, enterprises have put forward higher requirements for the forming process and product quality. The parts formed by the bending process not only have high precision of appearance dimension but also have good performance.
